Design Manifestos: Adam Tripp of Forms+Surfaces
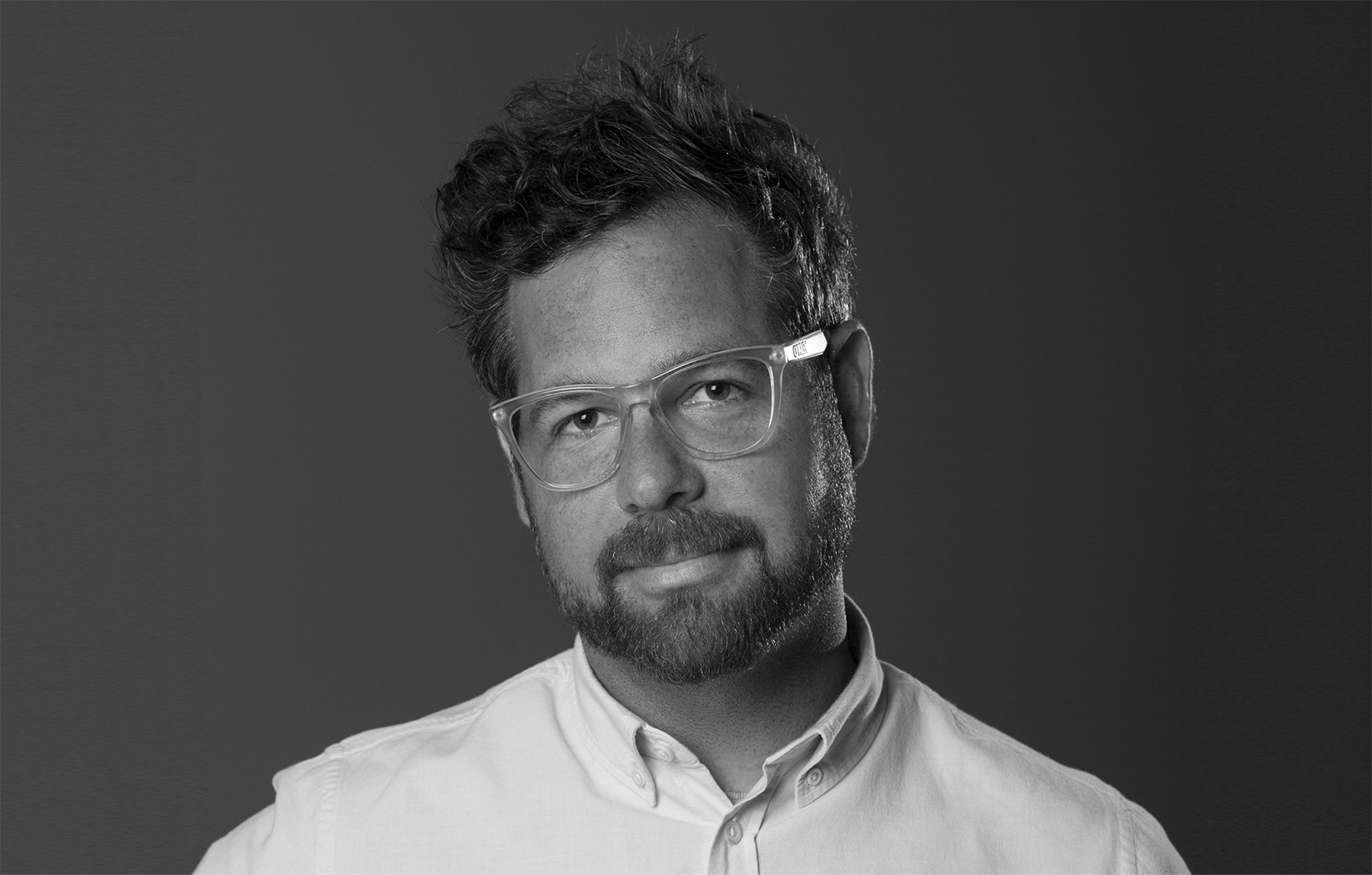
As Design Director for Forms+Surfaces, Adam Tripp oversees Product Design and Development across all F+S product lines. In addition to the project management of new and custom product development, he is continually defining new materials and manufacturing processes that influence the look and feel of the Forms+Surfaces brand. Adam is responsible for some of the most recognizable site furniture, architectural surfaces and door hardware in the F+S catalog. He joined the Forms+Surfaces Design Studio in Carpinteria, California in 2007 and holds a degree in Industrial Design from the Rhode Island School of Design. Modelo spent some time learning about how Adam discovered his voice as a designer and about the studio’s introspective approach to design.

On becoming an industrial designer
I’ve always been interested in fine arts, drawing, and problem solving through sketching. I consider myself extremely fortunate to come from a supportive and creatively diverse family of craftspeople who fostered and encouraged my skills from a young age.
As a child I would dream up and sketch ideas for vehicles built from old bike parts, boats, gliders and treehouses. I would bring those ideas to my father and grandfather who would take turns critiquing and red lining my designs. Unfazed by the critique I would revise and detail as many times as it would take to wear them down to the point where they would help and teach me how to make my ideas become reality.
The love for the process and being able to see an idea go from concept to built completion primed me for a love of, and career in, material and manufacturing exploration.
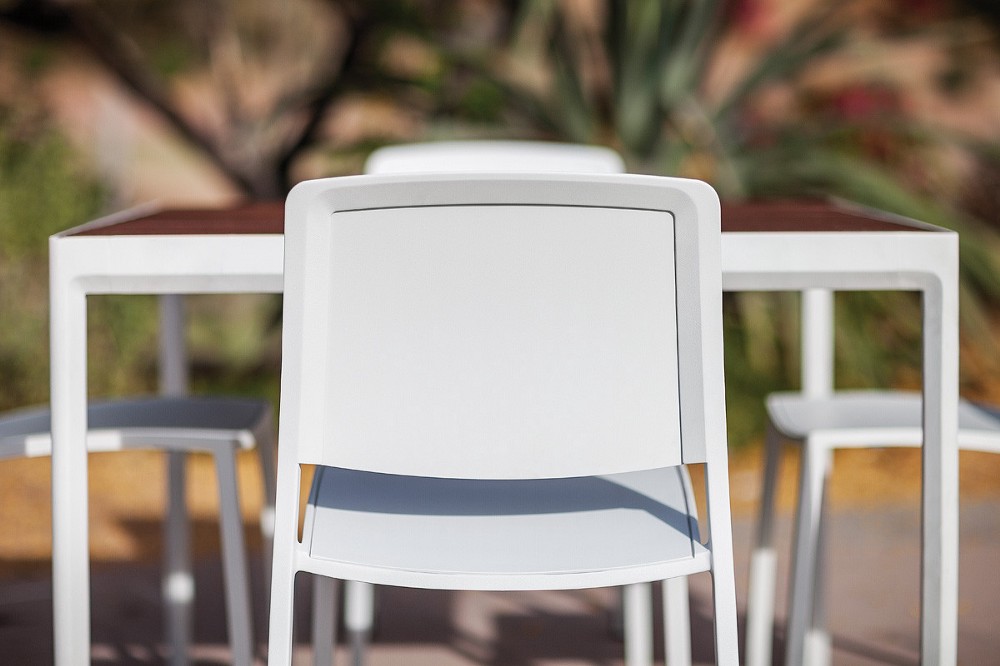
On discovering his voice as a designer
I always search to identify formal, visual and aesthetic relationships — inspirationally, critically and within my own work. This constant evaluation was on overdrive during my undergrad years at the Rhode Island School of Design. The high level of competition and inspiration there drove me to further identify my voice as a designer to distinguish myself from my peers. Although I like to think that RISD was a catalyst, I also like to think that I’m continually re-evaluating my voice based on my professional experiences and growing network of colleagues and mentors. Inspiration is everywhere.
On joining Forms+Surfaces
I had an opportunity to interview with Forms+Surfaces in Pittsburgh not long after graduating. I originally didn’t have interest in moving away from the east coast, specifically Providence, Rhode Island, but at that point in my career, I wanted to keep my options open and take all the interviews that were available to gain experience in presenting myself and my body of work.
Upon arrival I was given a tour of the headquarters and manufacturing plant. What I encountered was a manufacturing atmosphere at a scale and diversity I had never seen before: an Industrial Designer’s fabrication playground with large format laser cutters, milling machines, turret punches, and manual and robotic welding work centers, all grounded by a 2,500 ton, 40’ tall Hydraulic Press affectionately named Bertha.
My interview was interrupted by one of the F+S principals who described how it would be my job to break every machine I saw on that tour, pushing each to its limit with the goal of creating products and details that others could not. I was sold. I moved out to the company’s California office two weeks later and have embraced that same development philosophy ever since.
Having not been trained within an architectural discipline, but instead choosing a career designing solutions for architects, landscape architects and interior designers focused on manufacturing quality and sustainability first and foremost, I feel like my approach to architecture and landscape architecture changes on a weekly basis based on my interactions with practicing professionals.
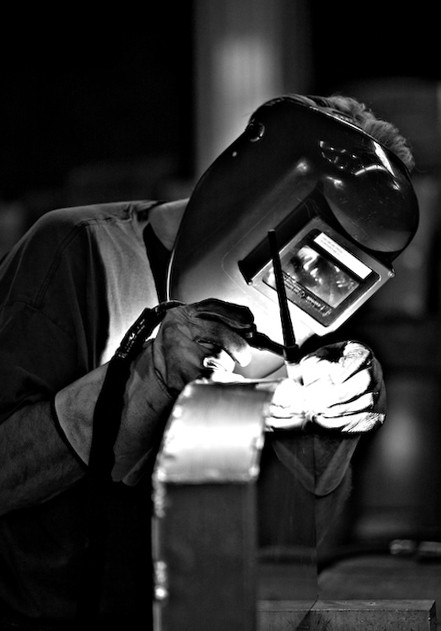
On specific principles he strives to adhere to
Our design studio exists in a cyclone of constant evolution. We challenge introspective rethinking and constant consideration of how we can grow together to encourage better organization, accountability and communication.
Standard principles which are constantly thrown around the studio:
- Make/destroy/make again — Fail fast
- Sustainability through quality
- If you’re not asking questions you’re not learning
- Do your job
On his role as Design Director at Forms+Surfaces
As Design Director, I’m responsible for standard product development through material, process and creative direction. I work as a brand ambassador through monthly visits to landscape, architectural and interior design firms across the country. These meetings give me a chance to showcase our in-progress concepts and seek out inspirational thought-leading discussions regarding the future of architectural product development and the evolution of public space.
Every month I also visit at least one of our North American manufacturing centers to check in on product production and development, take meetings and review progress with Design and Development team members.
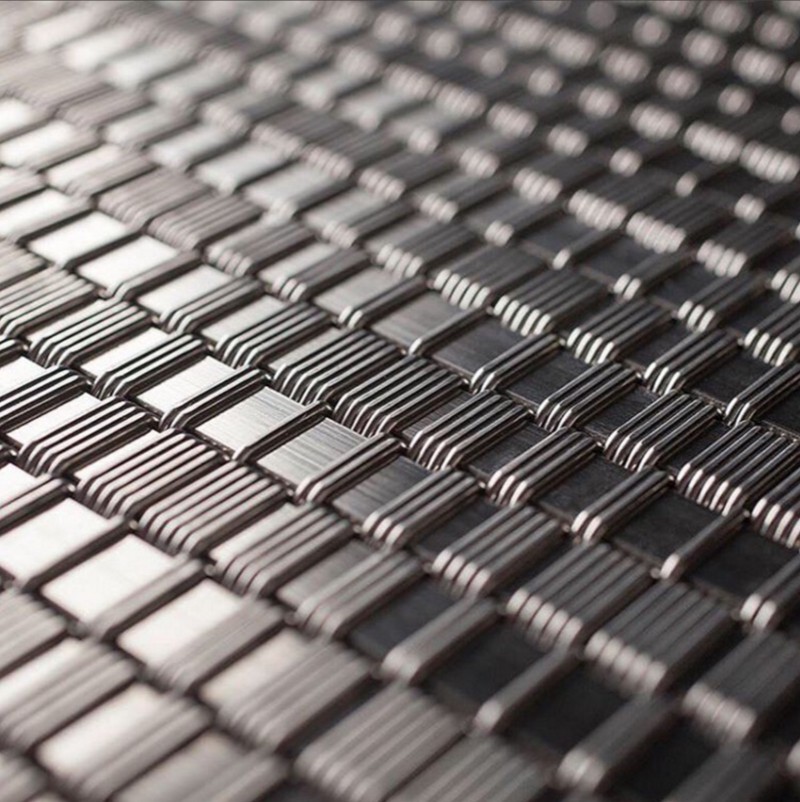
On recent projects that represent the firm’s unique approach
Above all, we’re Solutionists.
I’ve been given the unique opportunity to build a design and development studio tailored to the needs of a growing business with an extremely diverse product offering. Our studio is structured to be a collaborative environment that supports the multiple market segments we serve. Studio expectations demand that all our team members work simultaneously on multiple products across our different divisions: surfaces, systems, site furniture and lighting. We also have the luxury and the challenge of making the most of our extensive manufacturing potential — something we’re able to accomplish by utilizing design and engineering roles interchangeably throughout our process.
We’re currently putting the finishing touches on our new Design Center in Carpinteria, California. The space will serve as both a showcase for our standard products, as well as what will be an ever-evolving proving grounds for new products and prototypes. Highlights include 80 feet of continuous double-sided etched and graphic laminated art glass for a bank of managerial offices, and a full wall within the design studio dedicated to new systems and surfaces prototyping and installation.
On his design toolkit
Processes differ depending on which market(s) and products are being developed but the general outline for development within the studio is as follows:
- Research,
- Sketching (hand/digitally),
- Group evaluation (Repeat),
- Modeling (Repeat),
- 3D printing (Repeat),
- Prototyping at full scale (Repeat)
Moving directly from sketches and small prototypes to Solidworks allows our group to intersect directly with our standard engineering resources, 3D printers or CNC equipment at any point within the development stream.
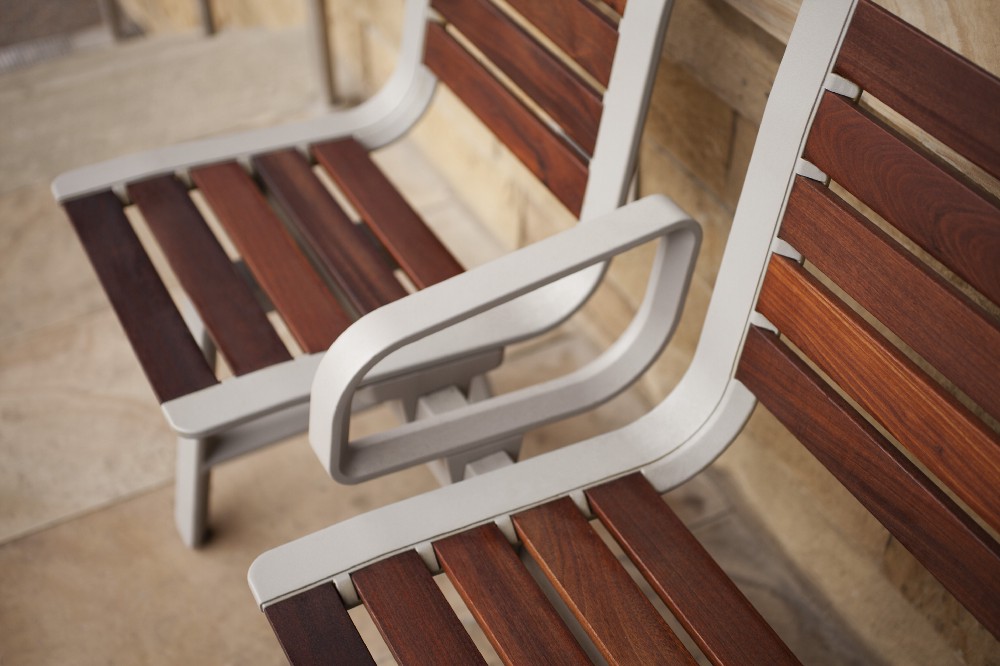
On the state of design software today
The pace at which new design software allows the process to move is ever increasing. Facilitating ease of movement from digital sketch to model to 3D print — to full assembly file — to production is a necessity that allows us to stay ahead of the curve and keep the fast pace of development we encourage.
On the future of the industry in the next 5–10 years
I think the industry will need to focus on the importance of personal and public space and the blurred lines between traditional architectural and landscape environments. As we continue to become ever connected to a digital world there will need to be a focus on interconnectivity within public space in the same way that if exists in most private and personal spaces. Blurring lines of technology between interior and exterior public space will be the next frontier.
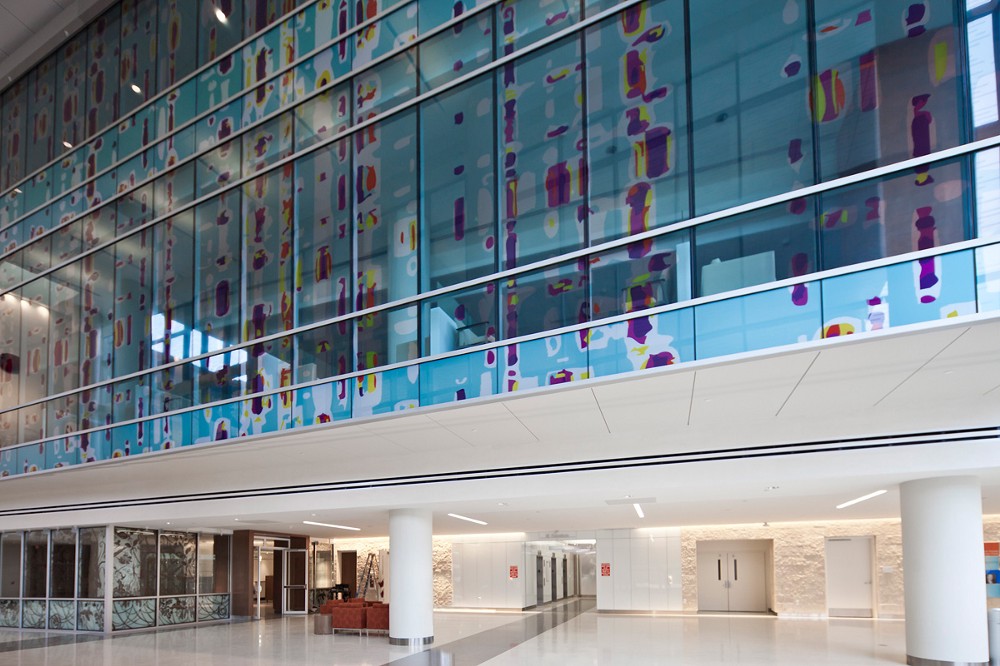
On the future of the firm in the next 5–10 years
Forms+Surfaces has been providing solutions for separate markets within public spaces large and small for decades. Our relationships with industry leaders and the ability to cross-pollinate diverse market resources has our company primed for the future of public space.
Adhering to our core values of honest material use, sustainability and quality will continue to carry us forward as we work to fabricate the changing landscape of public space in real time.
On advice he would give himself
Understand the resources at your disposal: experts love to talk about their respective expertise; you just need to identify the opportunities and ask.
Take every chance you can to reach out and expand your knowledge base. The more arrows in your quiver, the more prepared you are for future challenges presented.