Design Manifestos: Jason Flannery of TAKTL, LLC
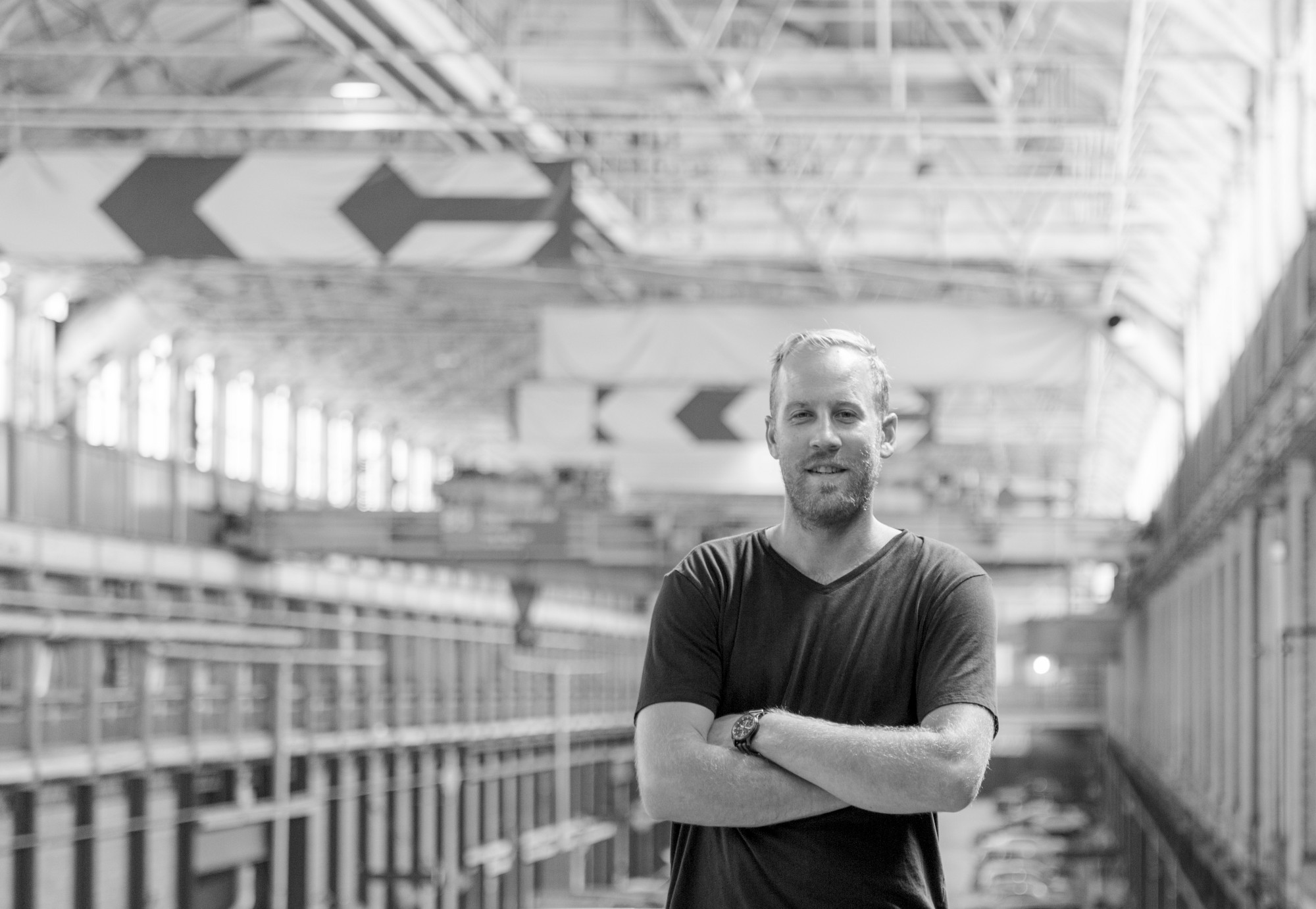
Jason Flannery is the Design Director and founding member of TAKTL, a leader in the manufacture of Architectural Ultra High Performance Concrete (A|UHPC) and VECTR Research, a newly formed research and development company focusing on the advancement of UHPC in architectural, commercial, and industrial applications. He divides his time between providing technical consultation for clients, designing equipment, tooling, and product solutions for new UHPC applications, and collaborating on VECTR research and development projects.
Prior to joining TAKTL in 2010, Jason led the Design Studio at Forms+Surfaces, where he oversaw product development in site furniture, lighting, and architectural surfaces+systems, and designed numerous successful product lines. As an Industrial Designer, his expertise in materials and manufacturing methods has allowed him to explore emerging technologies and eventually led to a growing interest in Ultra High Performance Concrete and its potential for architecture and design. Jason received a BA in Industrial Design from the Rhode Island School of Design. Modelo spent some time learning about Jason’s unique approach to design and about his role at TAKTL.
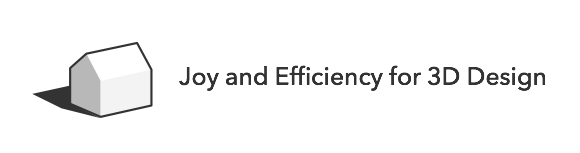
On becoming a designer
I have always been drawn to mechanics and problem solving. When I was growing up, we lived on an old farm and there were always things to be repaired or tinkered with. My family is in the architectural fabrication business which, from a very young age, gave me a lot of exposure not just to fabricators but also to architects, drafters, mechanical engineers, and of course, industrial designers. In high school I was leaning more towards mechanical engineering or architecture simply because I didn’t understand exactly what industrial design really could be. As soon as that became clear, everything clicked into place and I have never looked back.
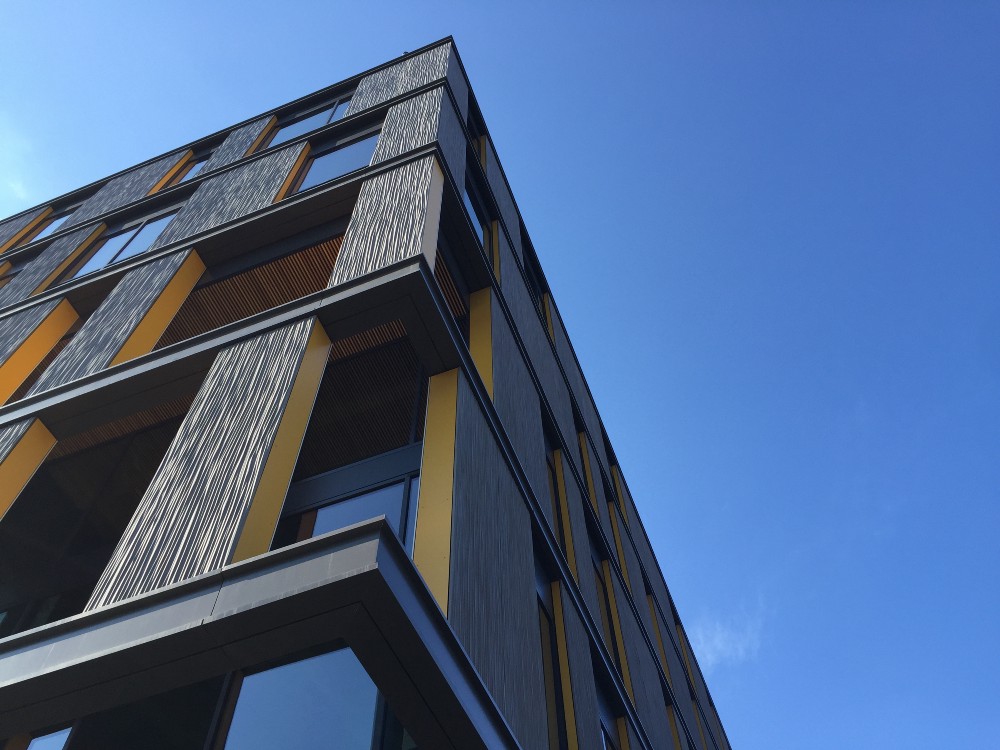
On discovering his voice
It is difficult to describe a fixed moment in time when I discovered my voice. For me it has been, and continues to be, an evolution. As a young designer I treated each project like it was going to be the last design I ever did, and therefore I had a tendency to try to pull in every unique idea I had. I remember one of my professors and early mentors, Mickey Ackerman, pulling me aside and telling me that I had a whole life of design ahead of me and that I really needed to just pick one thing and let that singular detail or bit of engineering speak for the whole project. As simple and obvious as that seems, at that point in my evolution, it was a game changer.
As far as influences, I have had many, although few of them the big name designers that you might expect. Early on I was lucky enough to work with both Paul Tuttle, a furniture designer, and Will Prindle, an industrial designer, while I was still in high school. Both were true old school practitioners and really exposed me to the craft of design. I think that it was my friendship with them that really steered me in the direction of design in the first place and in the case of Will, who had a strong connection to RISD, also to the industrial design program there.
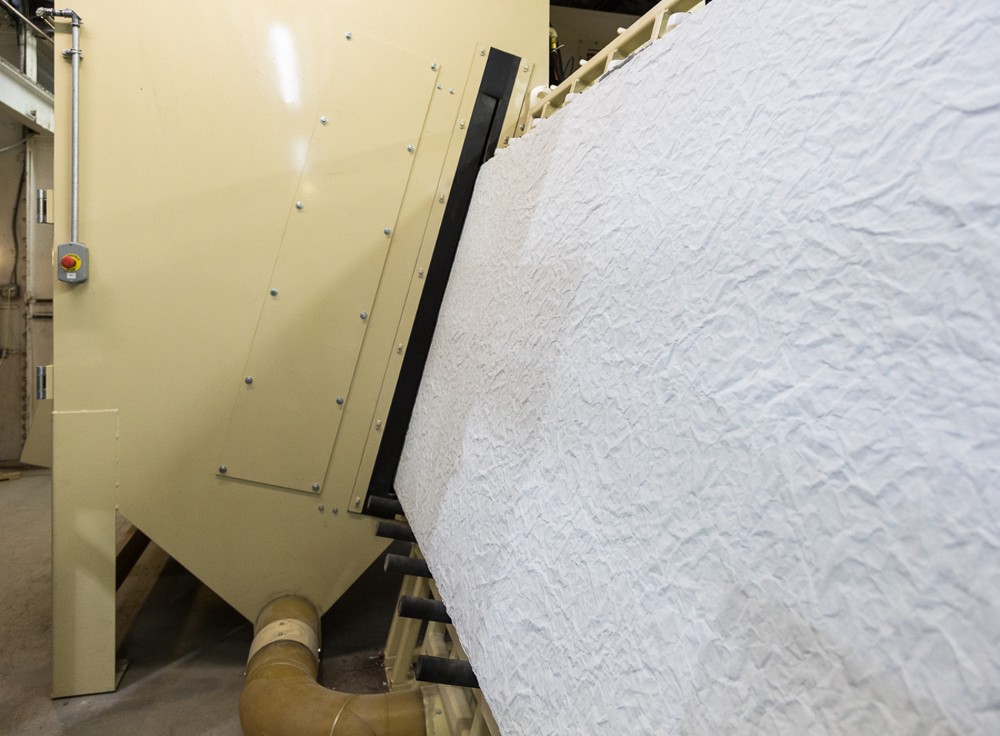
On joining TAKTL
I was involved in the original UHPC research project at our previous company, Forms+Surfaces, where I was leading the design studio. That project was successful enough that we decided to launch TAKTL as a separate company. For me the draw towards working with a relatively new and uncharted material and process was very strong. Also I liked the idea of really putting all of my focus into the advancement of a singular material. As designers, we have to develop an understanding of a wide range of materials and manufacturing technologies, and this was particularly true for me in my first ten years of design, so I definitely benefited from the approach. However, it is very rare that we get the opportunity to really focus all of our energy and creativity on one material and a few select processes and see how far they will take us. This experience has had a huge impact on how I work and also my willingness to take on all aspects of a design project.
On specific principles he strives to adhere to
In general I try to adhere to the core belief that design should be honest and focused on addressing actual needs. Beyond that I am a material nerd. There are very few materials that I inherently dislike, and I really enjoy the process of identifying the right material and manufacturing methods for a given problem. This kind of intersection between material characteristics, price, environmental considerations and aesthetics is what I’ve found to spark some of my best creative thinking. In my job, I see too many designers fixate on a material that isn’t a good fit for the application.
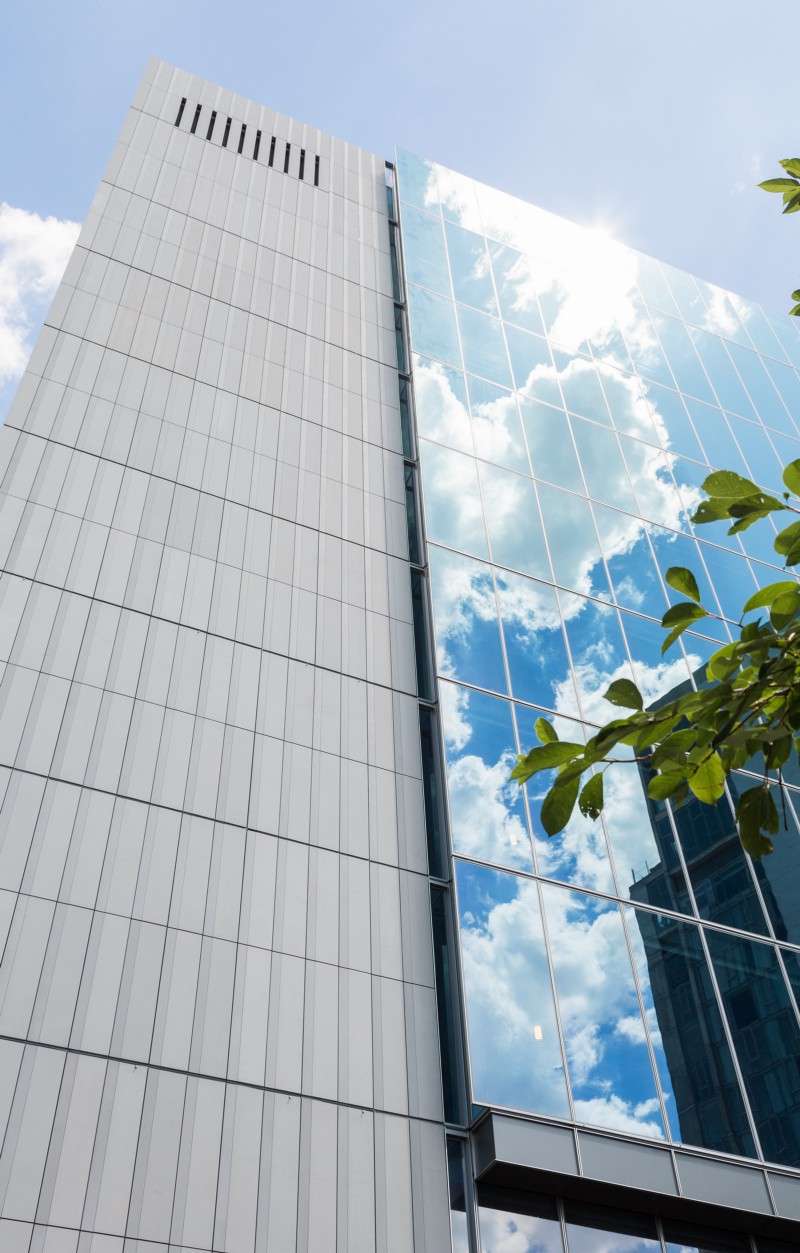
On his role as Design Director
The primary role I have is a forward looking one and includes everything from assisting clients in resolving complex design issues through process ideation and the development of new materials/ product lines and the requisite manufacturing equipment.
On recent projects that represent the firm’s unique approach
By necessity we have a very unique approach to design. When we first started down the road to manufacturing UHPC elements with a high level of finish it was apparent from the outset that there were very few resources available to us both in terms of body of knowledge that we could tap into as well as manufacturing processes and equipment that we could deploy. As a result, we began to develop those resources and equipment in house. In fact, the design portion of our research and development arm has evolved into a full time staff of engineers, industrial designers and fabricators dedicated to the design and manufacture of unique, process-specific equipment — everything from specialized mixing equipment, molds, and casting machines, through material handling and secondary processing equipment. This allows us to explore manufacturing concepts very quickly and cost effectively as well as design equipment and processing lines specific to individual product or customer needs. As a designer, this holistic approach to design ideation through manufacturing and marketing has been extremely effective and rewarding.
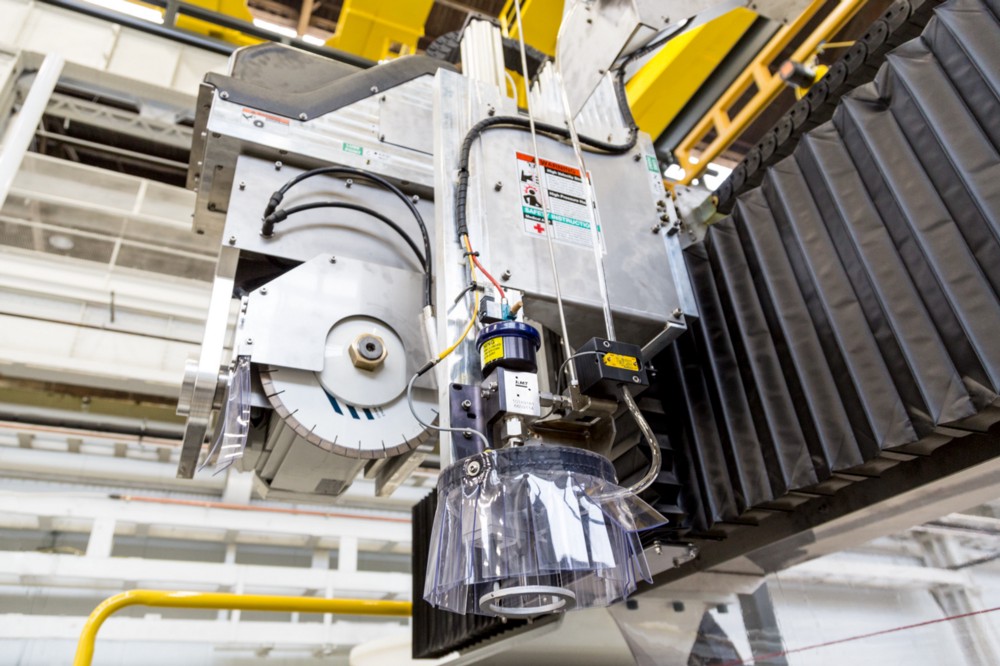
On his design toolkit
I use a combination of sketching, 3D cad, and physical prototypes. In general I would say that I am very quick to go from sketching into the CAD and physical prototyping stage. There are just so many problems than can remain hidden until something is realized in “real” dimensions. As far as computer software, I use SolidWorks as the primary 3D software, Rhino and AutoCAD for interface with the architecture market, Maxwell for rendering and Adobe CS for graphics and pattern development.
On the state of design software today
I think that the current state of design software is pretty amazing! The ability to flush out complex geometries and mechanical solutions and move those fluidly through the prototyping and revision process has really streamlined the design process. That said, within the architecture market I think there is still a lot of room for improvement. Most of the software is centered on the needs of the designers and contractors, not the manufacturer. This is especially true as building geometries and construction methods have become more complex.
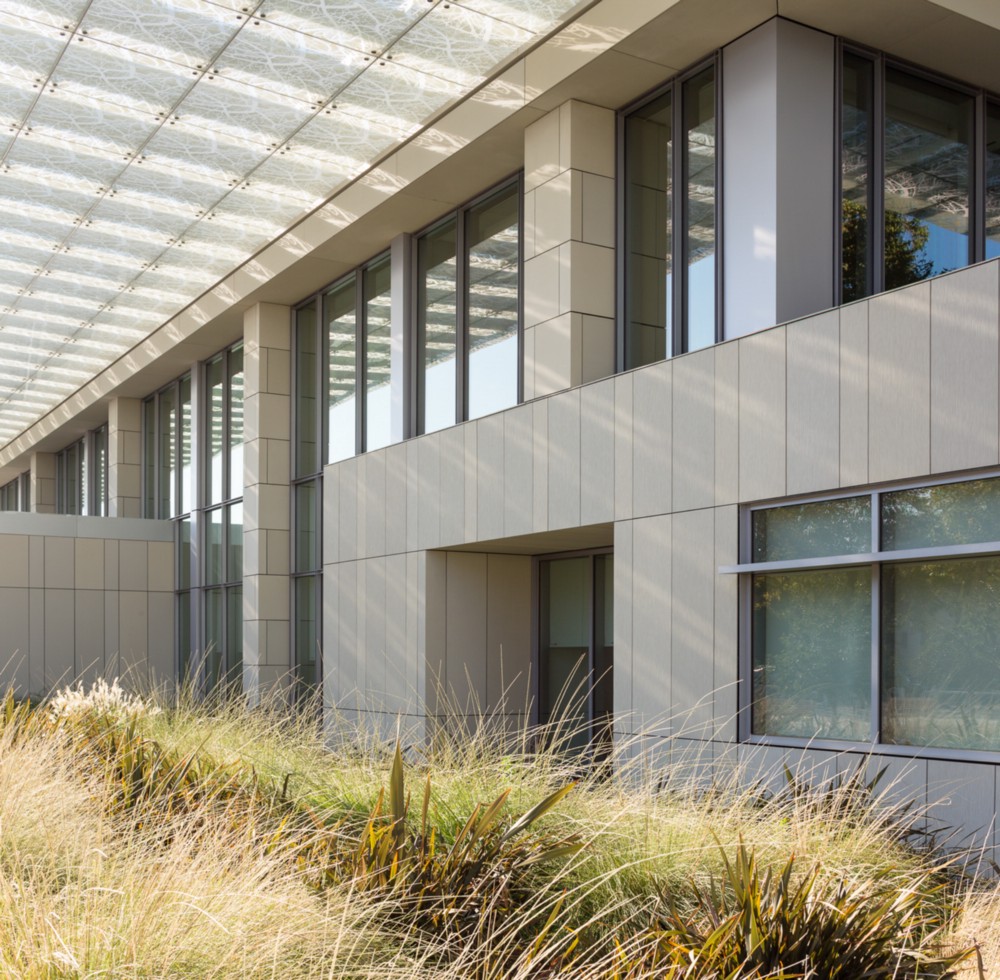
On the future of the architecture industry in the next 5–10 years
This is an interesting time for architecture, especially regarding high performance facades. In the last few years some of the primary markets such as New York and the Bay Area have really started to embrace ventilated rain screens in the face of changing energy efficiency and building standards. Looking forward over the next few years, I believe that momentum will continue into a more wide spread adoption.
Specific to UHPC, the change has already been significant. Just five years ago there were very few architects in the U.S. who had worked with UHPC. Like any other “new” material there is a learning curve to really maximizing its potential. Now that we are working with architects on their second and third projects we are really starting to see a better understanding of how the material can be used and pushed in new directions.
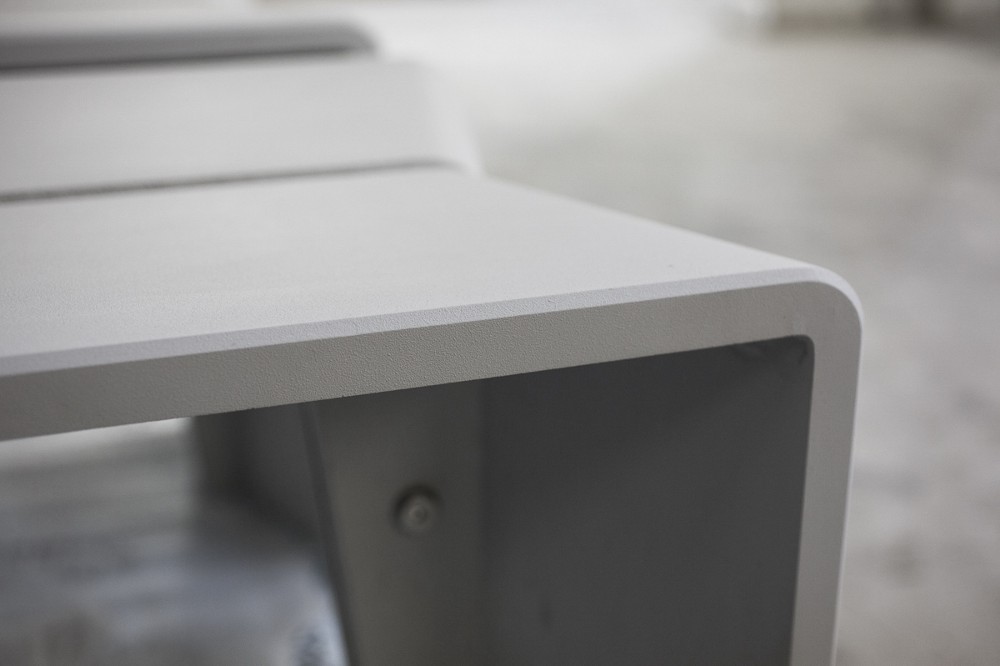
On the future of TAKTL in the next 5–10 years
TAKTL is a design centric manufacturing company and as a result we try to stay fluid enough to respond to the needs of the market in the moment. We spend a lot of time looking at design and construction trends and trying to anticipate what solutions might be necessary ahead of time. We are really dedicated to advancing the use of UHPC in architecture, and to this end we have set up a pretty robust research and development group. I can’t go into too much detail about some of the projects we are working on at the moment but let’s just say that we are really excited the new directions in both material technology and design.
On advice he would give his younger self
Expert opinions are valuable but shouldn’t be the last word. I think that very often the best ideas sound completely ridiculous on first hearing them, simply because we don’t have the right frame of reference to understand them. As a result they are pushed to the side in favor of more conventional approaches. In my early career I didn’t have the confidence to stick with those disruptive ideas, and I let them drop…only to watch someone else down the line pick up run with them. In our design group we always joke about a “river of tin” in reference to the manufacturing process for float glass in which the glass is cast onto a giant river of molten tin. There is some humor in imagining the presentation of that idea and how impractical it must have seemed and yet it is still the same basic process used 60 years later.